This will show you how to wire some LEDs to add some light to your rig.
In this tutorial, I show how to create a light string with two bright red LEDs. These are going to be wired to a plug that you can connect to your receiver to power them up.
The plan is to end up with a servo plug going to a length of wire to an LED, then another length of wire to the other LED. These could be installed as a pair of brake or tail lights, or use white LEDs and you could have a set of headlights.
For some, this is fundamental stuff. For others, I hope this helps answer some questions and encourages you to build your own set of lights!
An overall view of the materials to be used.
Side cutters, needle nose pliers and wire strippers.
Two lengths of stranded wire (I think it is 22 gauge) that I recycled from an old network cable.
Two LEDs
Two 150 ohm or 220 ohm resistors
Some heat shrink
A servo cable cut from an old servo
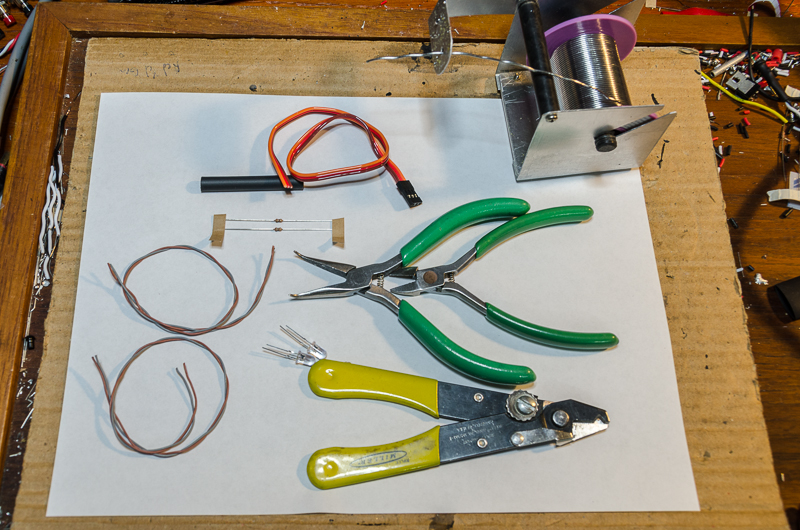
The LEDs need a resistor to limit the current flow or you risk burning them out or limiting their life. The two resistors shown here are 150 ohm (colour code: Black, Green, Brown, Gold).
LEDs are polarity-sensitive devices. This means they will only pass current flow in one direction. The LEDs have a few ways of telling you the polarity of their leads. There will be one lead shorter than the other, and that one is negative. Often there will be a flattened area near the leads and that also indicates the negative lead. I have clipped the negative lead of the upper LED and one end of each resistor.
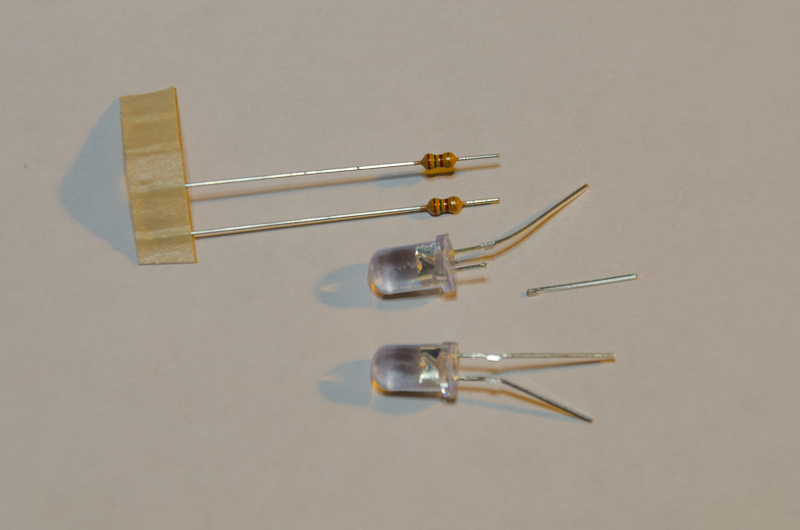
Here you can see that the upper LED has been soldered to one of the resistors. To do this, I first tinned the areas I wanted to solder and then held them together and added a little heat until the tinned bits flowed together.
If you are wondering if these parts are heat-sensitive, the answer is yes. The resistors can tolerate the heat well, but be quick on the LED. A good idea is to hold the LEDs lead with needle nose pliers right close to the LED body. This will help keep the heat from passing into the LED.
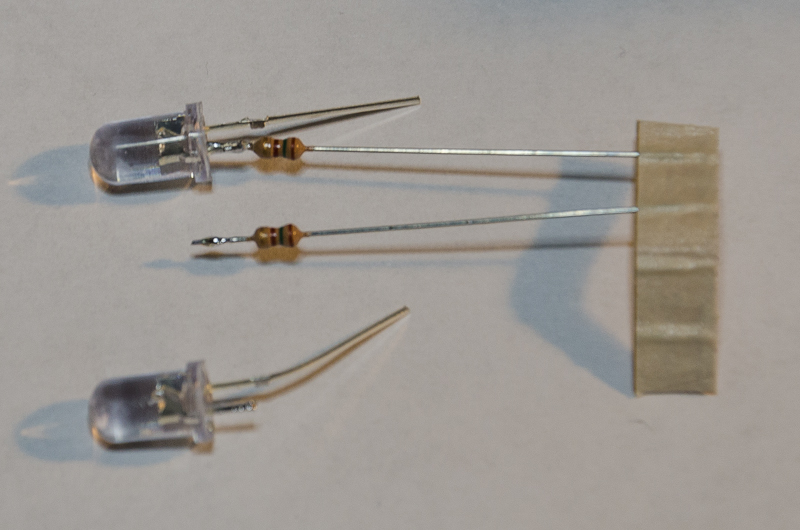
Both LEDs with a resistor soldered to their negative leads. The resistor is bent out like that to stop it from rolling over before I took the photo.
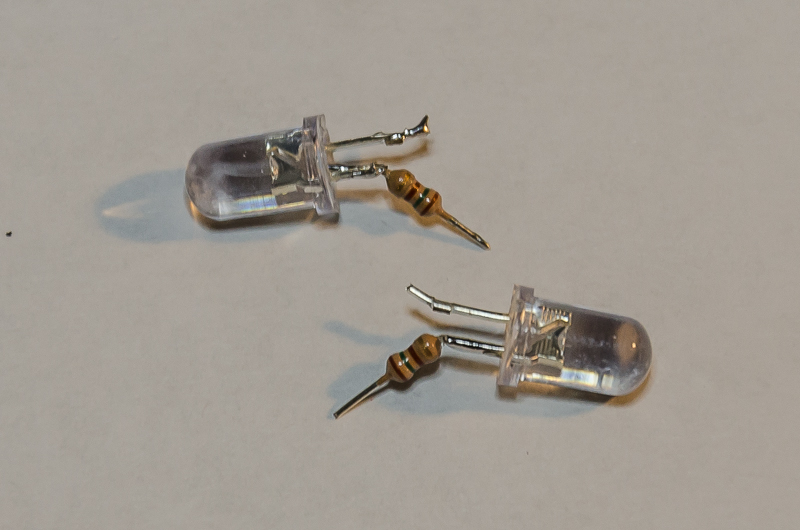
Prepping the wire for soldering... I've decided that the grey will be negative and the brown will be positive. The wire length has been cut and the insulation has been stripped to match the components to be soldered. Again, tin the wires before soldering to make things easier.
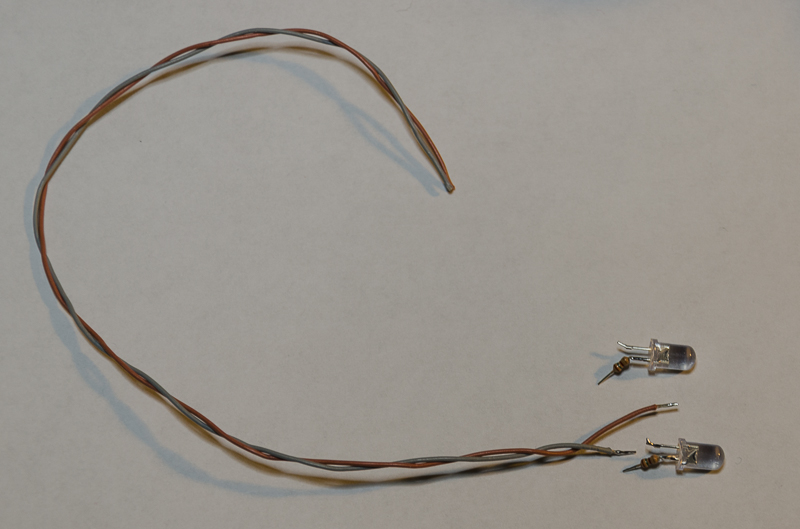
Notice that because of the way the components are placed, even if the leads are pinched together, there won't be a short circuit - at least, it helps to minimize the risk. Better yet would be to place heat shrink over one of the wires but as you will see later, I'm doing it differently.
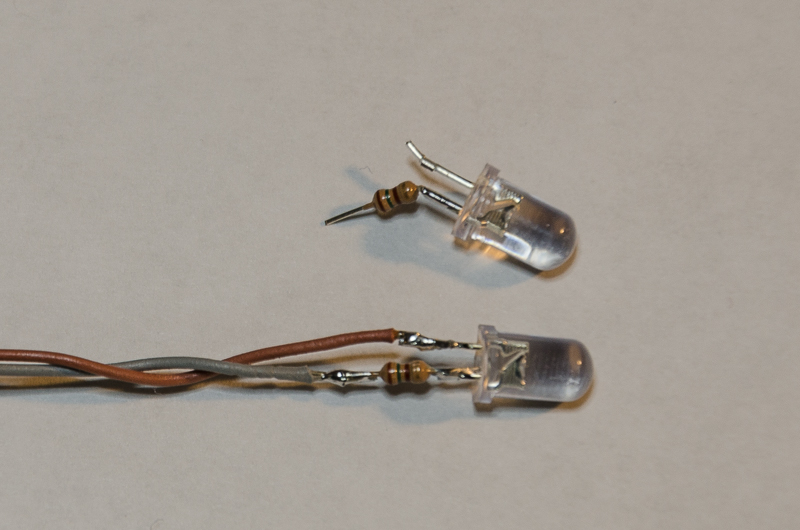
The wires are cut to length, stripped and twisted together.
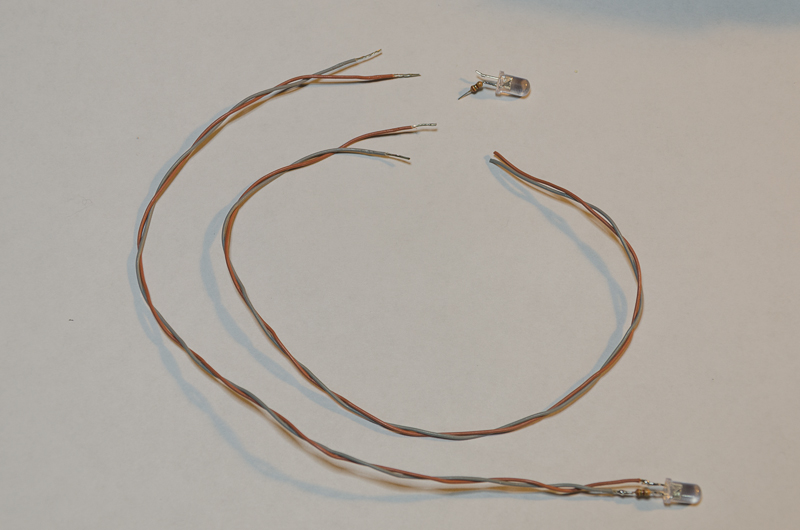
Tin the wires and cut the ends off cleanly.
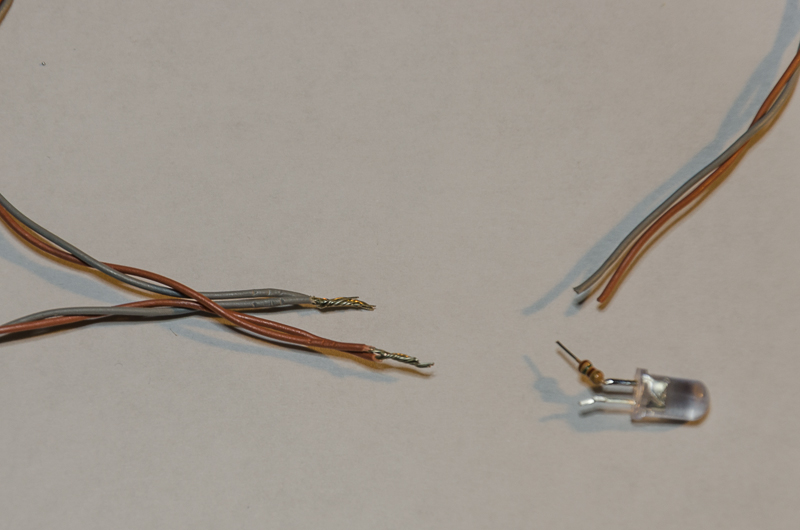
The double wires make things a little bulky, but it will work out.
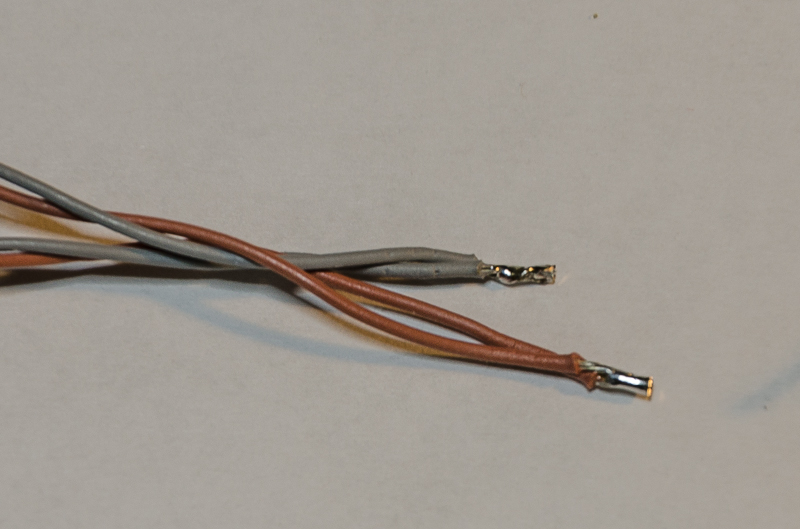
So far, so good.

Make use of the old servo cable.
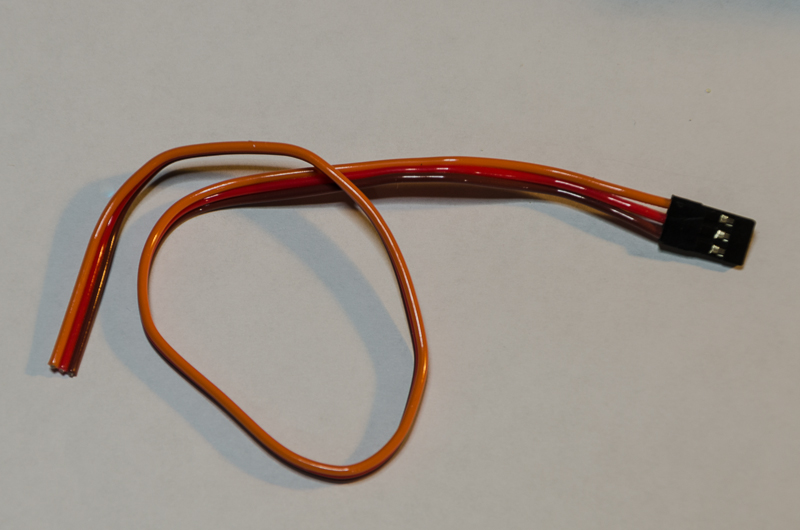
The signal wire in this cable serves no purpose for the LEDs so it gets snipped right next to the plug and then peeled right off.
Prep the wires for soldering. Remember that grey is negative. Don't forget about heat shrink (yes, I'm using it here). Also note how the wire lengths are staggered to help reduce the chance of shorts.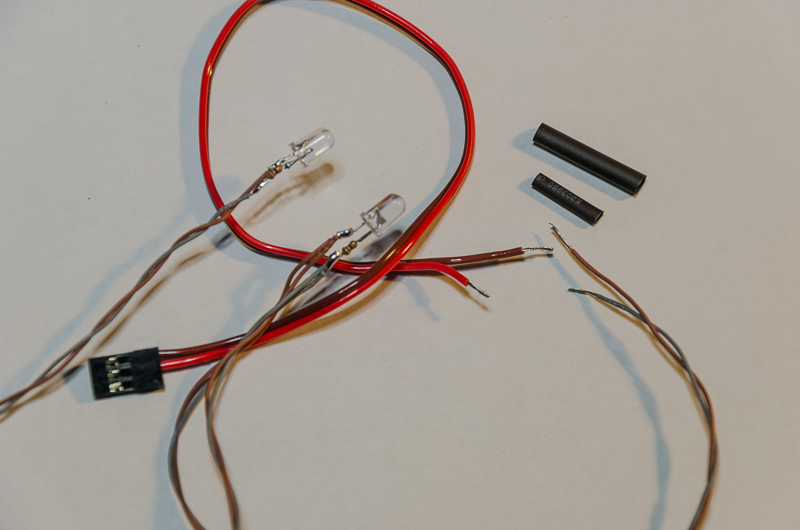
Slide the heat shrink onto the wire before you solder that connection (I still forget to do that sometimes!). In this connection, I have slid the thin heat shrink over the grey wire only and the thick heat shrink is slid over both wires. Slide the thin shrink over the soldered connection and shrink it. Then slide the thicker shrink over both the thin shrink and the other connection.
Heat shrink is cut to length to cover up the LEDs and resistors. This size of heat shrink won't easily fit over the LED so I stretched it a little wider by sliding it over my pliers and opening it slightly.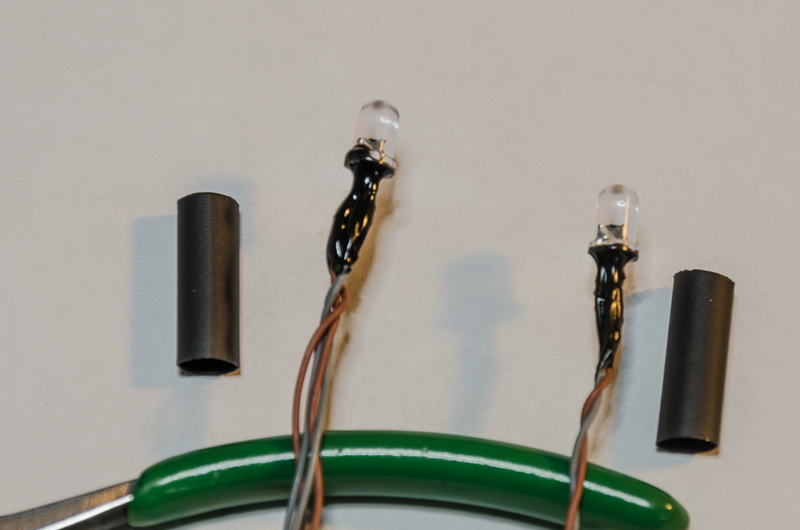
A coat of liquid electrical tape or plasti dip is how I have chosen to insulate around the resistor and LED junction before the heat shrink goes on.
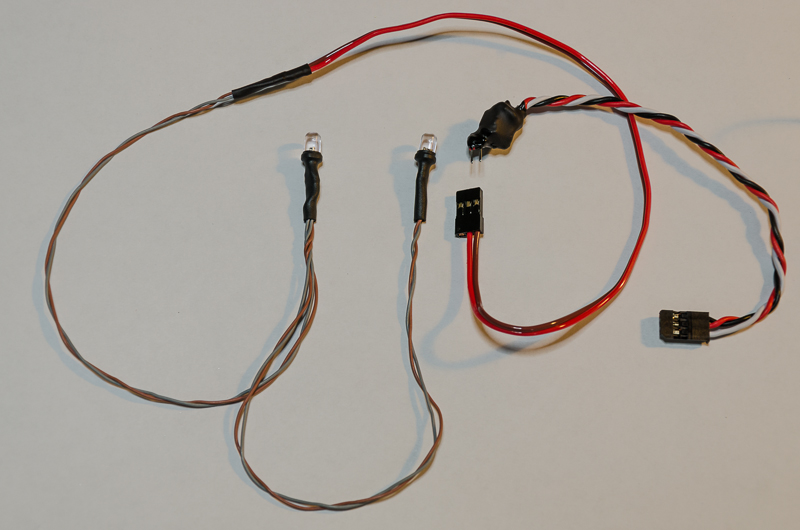
Heat shrink in place and showing off some light!
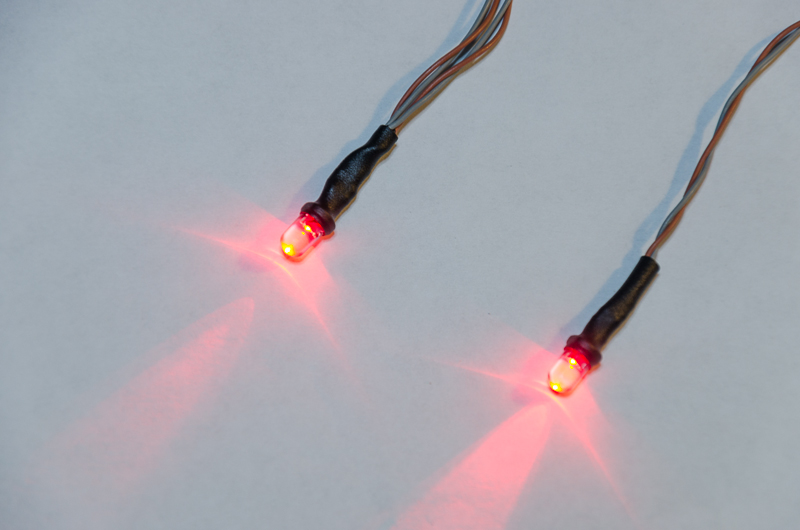
The completed LED string. Shown next to a
https://www.heyokperformance.com/Remote_Switch_for_LED_Lighting/p1742582_8014063.aspxthat could be used to remotely operate the lights.
Happy lighting!
Al